Todays Update
Well, in order to measure the iron carriers internal dimentions, I needed to remove the pinion. This should be simple enough.
You just hold the drive flange in a vyce, undo the big nut on the pinion, pull the flange with a puller, then gently knock the pinion out with a soft hammer or push it out in a press. Easy peasy.
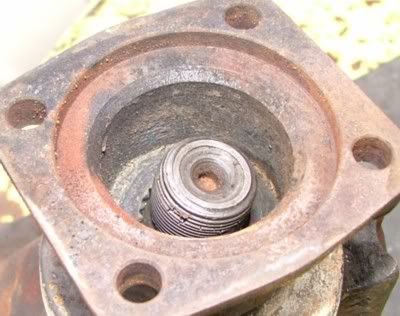
Oh dear lord, if only it were so. Well, the nut came off easy enough, but that was the last easy thing it would let us do.
The flange did not come off with a few bumps from a copper hammer.
It would not come off with a sturdy puller either, so we decided that it must be rusted on. Perhaps a little push in a press would dislodge the pinion from the drive flange & the internal bearings in one go, so we set it up on a 65 Ton press, placed a 1" diameter slug of steel on the threaded section & started to press it.
At more than 30 tons, it became obvious that the short steel slug was bending, so we gave up & saw that the threaded section was bent also.
Next, we added a little warmth to the drive flange, still convinced that this was the problem. We warmed it untill it glowed red while adding some pressure with the press. Still no action.
<---- see picture.
Next, we removed the drive flange with an oxy torch. This should do it, so when we got it off we hit the pinion a few times with the hammer. Nothing.
So we cooled it all down & stuck it in the press again. At about 20 tons, we knew it was not coming out.
Next, we cut the inner cone down two sides right through. Surely this would do it, but no, even the press wouldn't shift it, but we were working on much lower pressures now. If it didn't come with a few tons, then it wasn't coming at all.
Next we cut the bearing cone all around its circumference to blow away the rollers & this finally allowed the pinion to come out, but with the remains of the inner bearing cone still firmly attached.
Once it was on the bench, we were able to break up the remains of this cone to reveal the real reason for all this drama.

This picture shows the pinion with a small piece of the inner bearing cone at the bottom of the picture.
While it isn't visible in the picture, the splines on the pinion are actually twisted ever so slightly. This is what was preventing the drive coupling from coming off, but we think that it would have come off in the press OK if we had tried to remove it by itself.
The mark in the pinion, where the bearing sits, & the corresponding mark on the bearing remnant is the cause of all of our grief. The bearing locked up at some time, probably just after it ran out of oil when the drain plug fell out, & the pinion spun inside the bearing, welding itself to the cone. At this point the diff, somewhat unsurprisingly, siezed. It was this pinion shaft welded quite solidly to the bearing that would not allow the damn thing to come apart.
Fortunately, the diff carrier is undamaged, although the paint is burnt, & is suitable for measuring as was originally intended & I will do this in the next couple of days.
To top it all off, I weighed the two carriers on a rough & ready spring scale. The alloy one came in at about 5-1/2lb [2.5 kg] while the iron carrier [without caps] weighed about 14-1/2 lb [6.5 kg] so at about 9lb [4kg] the weight saving was not as much as we had hoped for, but it's too late now, I will complete the measuring & let you know the results.
If it's all good, I will put the alloy carrier aside, discard all the iron diff parts & continue on with my own car & just hope that the bearing caps show up.